This is the fifth post in our series from our Thermoforming Handbook, a guide that, until now, was only available to our customers and partners. We’re releasing the whole thing in a series of posts right here on our blog.
We’ve previously released:
- Chapter 1: An Overview of Thermoforming
- Chapter 2: Designing for Thermoforming
- Chapter 3: Tooling, The Foundation of Thermoforming
- Chapter 4: Thermoforming Materials Selection
If you’re someone who uses custom plastic manufacturing professionally and you’re interested in getting your own copy, just send us a message and we’ll be happy to send you one. As always, these are general guidelines. Any project or design needs to be reviewed by a qualified thermoforming professional before it goes into production, and the sooner you get one of those qualified professionals involved in the process, the smoother things tend to go. If you’re looking for a qualified professional, we know a few who would be happy to help.
Open up an engineering textbook, and it’ll likely define tolerances as the “permissible limit or limits of variation.” To put it more simply, how close to your exact specification can you expect the final product to be?
Every manufacturing process has unique tolerances, and thermoforming is no different. It’s important to note that what we’re listing here are industry standard thermoforming tolerances. If you have a project that demands tolerances tighter than what is standard in the industry, we’d be happy to hear from you. Our team loves a good challenge.
But with that out of the way, let’s take a look at industry standard thermoforming tolerances.
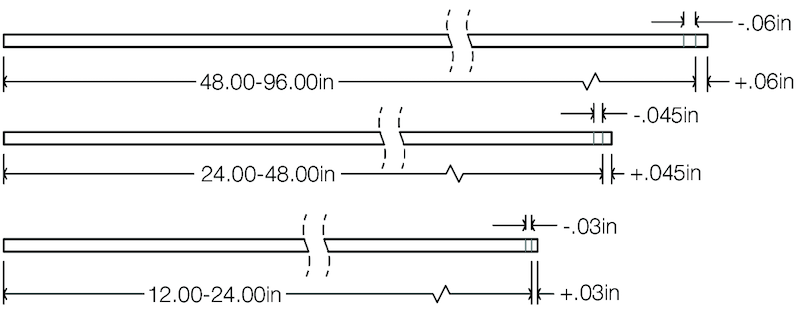
Activity | Tolerance | Guideline |
---|---|---|
Formed Measurements | ± .020” | Additional .001 Per Inch Beyond 12” |
Drilled Hole Diameters | ± .005” | Holes Equal or Lesser Than 1” |
Drilled Hole Diameters | ± .010” | Holes Greater Than 1” to 5” |
Slots | ± .010” | Slots Equal or Lesser Than 1” in Any Direction |
Slots | ± .020” | Slots Greater Than 1” |
Robotic Trimming | ± .020” | Includes Hole Diameters Greater Than 5” |
Robotic Trimming | ± .020” | Trim Feature to Trim Feature Distance Is Greater Than 5” |