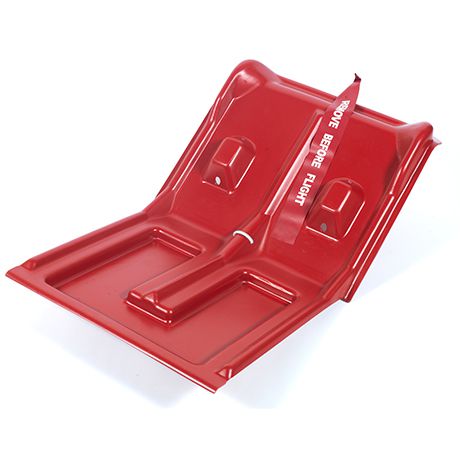
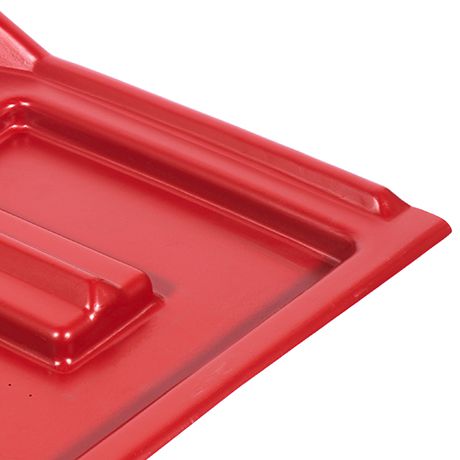
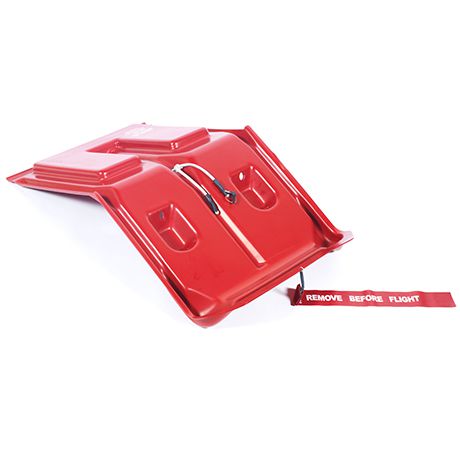
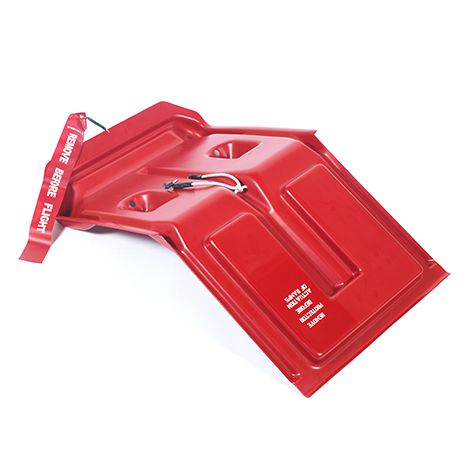
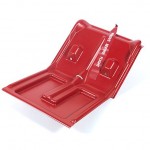
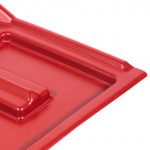
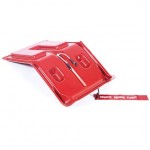
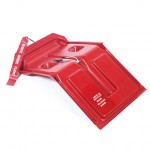
Reverse Engineering a 40-Year-Old Aircraft Part
INDUSTRY | Aerospace |
---|
Project Summary
An aircraft parts supplier came to us with a unique challenge. They were being asked to develop a replacement for a part that was last manufactured in 1972. The original molds for the part had long since been destroyed. All we had to work with was a sample part and a full-size drawing from 1972.
To create an exact replacement part, we used a combination of our history with traditional thermoforming practices and some cutting-edge 3D technology.
Project Details
In 1972, Ray Products had already been in business for more than 20 years. Even today, in an age of CAD files and computer modeling, our engineers know their way around a 40-year-old drawing. That said, the drawing didn’t give us all the data we needed to exactly replicate the original part.
That’s why we brought in our 3D technology. The FaroArm we use produces 3D models of real-world objects that are accurate to within .001 inches. By digitizing the sample part, we were able to convert a 40-year-old piece of plastic into a 21st century 3D model.
Next, we compared the 3D model created by the FaroArm with the critical dimensions from the part’s original drawing. Using this process, we were able to verify that the 3D model we had created was an accurate representation of the engineer’s original specifications.
Once our verification was complete, we used the 3D data to create a new, aluminum, temperature-controlled thermoforming mold. The new mold was created in under 6 weeks. Once the mold was complete, we had the first part sample, fully documented and inspected, submitted to the customer in less than a week.
The customer requested a few minor changes to hole diameters and trimmed slots. These were easy to accommodate, thanks to our fully robotic, six-axis trimming stations.
Today, our customer is able to cost-effectively offer an accurate replication of a part that was last manufactured when Richard Nixon was in the White House.
Download This Case Study as a PDF